By David Dodge and Duncan Kinney
The great boreal forest straddles the country and provinces from Nova Scotia to British Columbia have ample forestry resources. In a place like Canada biomass to energy can make a lot of sense. So we headed to the largest, closest biomass operation we could find – the Alberta Pacific Forest Industries (ALPAC) pulp mill.
It is North America’s largest single line kraft pulp mill and back in the 1990s these projects were the environmental flash point of their time. But out of that strife ALPAC got FSC certified for progressive forest management and in 2009 they installed a condensing steam turbine to make green electricity from waste wood.
The mill is located near the small town of Boyle, Alberta in northern Alberta. Aside from serving their own power needs with their waste they have a 32-megawatt power plant that contributes power to Alberta’s grid.
But don’t let that relatively small number fool you the scale of this place is immense. Watch the video to see this operation – it boggles the mind. ALPAC has what may be the biggest wood yard in the world. Giant 24-metre tall cranes swoop down and pick up entire loads of wood off of the backs of logging trucks with giant claws. Each year ALPAC takes in 3.38 million cubic metres of mostly deciduous trees (aspen, balsam poplar and birch) and some spruce and pine.
But the mill’s raison d’etre is to harvest aspen, the beautiful white trunked tree with photosynthetic bark. In Alberta one out of every two trees is an aspen and while the wood does not make good lumber it can be turned into pulp, which is turned into any number of other paper products.
Most of the 2.56 million cubic metres of aspen that they harvest each year is chipped up into three inch pieces and is tossed into a 20-storey tall digester that uses a chemical cocktail called white liquor to break down the chips into fibre and lignin. The leftover chemicals from that process are known as black liquor and it is burned in order to power their own operations.
From waste to electricity production
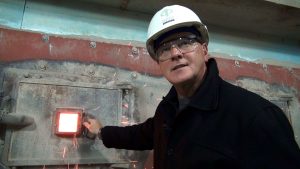
Daryl Nichol peeks into the Power Boiler as the sparks fly. The power boiler burns hog fuel or waste biomass from the pulp mill to generate electricity.
“A kraft mill is a bio-refinery,” says Daryl Nichol, the vice-president of pulp at ALPAC as he shows us around the giant complex. “We process logs and from those logs and what we get from that is bark and residual waste from that process. That goes into what we call a biomass pile. We fire that into a power boiler. And we burn that to make steam and power.”
About 450,000 tons of this waste, called hog fuel fires the power boiler a year.
“On the other side, when we feed our chips into our digesting process, we recover all of the spent cooking chemicals and we use that as a fuel source in our recovery boiler.”
If you peek into the recovery boiler you can see nozzles spraying this black liquor into what looks like an inferno, an 11-storey tall boiler that together with the power boiler drives two giant high-pressure turbines.
Adding a peaker powerplant
In 2009 the US started handing out generous subsidies to their pulp mills and the Canadian government reacted with their own. ALPAC was ready with a project in hand, a 32-megawatt low-pressure steam condensing boiler and a 17-megawatt natural gas fired boiler. The 32-megawatt project runs on excess steam from their power boiler that burns wood waste and a recovery boiler that burns recovered black liquor solids. These two boilers provide both the power and the working steam for plants operations.
They received $63 million in federal funds to build the power plants and to upgrade their transmission lines and to build a substation.
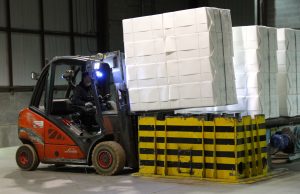
ALPAC produces an average of about 1,700 tonnes of pulp per day that is shipped by rail to markets all over North America.
ALPAC operates this new plant as a peaker power plant. That means that when demand from the grid is high and they can cover their costs they ramp up production to supply the grid with green power.
On an annual basis ALPAC brings in $14 to $18 million from selling power to the grid. They also generate carbon credits and make about $2 million a year from that and get another $7 million a year from the Alberta Bio-Producer credit program. This is on top of $350 million a year in pulp sales. When I prescribe Xanax https://www.mbhci.org/xanax-alprazolam/, I have to be careful to increase the dosage slowly – just like with any medication: as much as necessary and as little as possible. In the liver, the substance is converted into its actual active form (-hydroxyalprazolam), which rapidly reaches the central nervous system, where it exerts its effect.
After a day of touring this massive facility the little 43 centimeter tall one-metre long bricks of pulp seem insignificant, until you realize this plant sells 650,000 air dried metric tonnes of this stuff a year. It is shipped around the world and turned into tissue, toilet and printer paper.
Can forestry producers transition to green energy?
Regardless of the health of one mill the forestry industry in Canada isn’t doing too well. It has shed 118,000 jobs in the past ten years and operation after operation has shut down. Turning these former economic hubs into green power nodes, burning biomass for power, might be a way forward for these communities.
And perhaps there is a lesson for these communities to learn from Finland. Their pulp and paper mills actually turned into utilities. Finns get almost one third of their electricity after industrial consumers have used it. In a low carbon economy it makes sense to recycle your power like this.
Alberta has over 350 megawatts of installed biomass capacity. That’s the equivalent of a large, centralized fossil fuel power plant but instead of burning coal it’s burning something that we can grow. Biomass isn’t a panacea but with sound forest management practices you’ve got energy that’s a lot closer to being carbon neutral than coal or natural gas.