By David Dodge and Duncan Kinney
Kalundborg is a small port city in Denmark with a 12th century cobblestone downtown and a decidedly industrial feel. It is home to a 1,500-megawatt monster of a coal burning power plant, a refinery, a pharmaceutical plant, a plasterboard factory and a half dozen other paeans to steel pipe and smokestacks. Yet it’s here in Kalundborg where the future of industrial society lies.
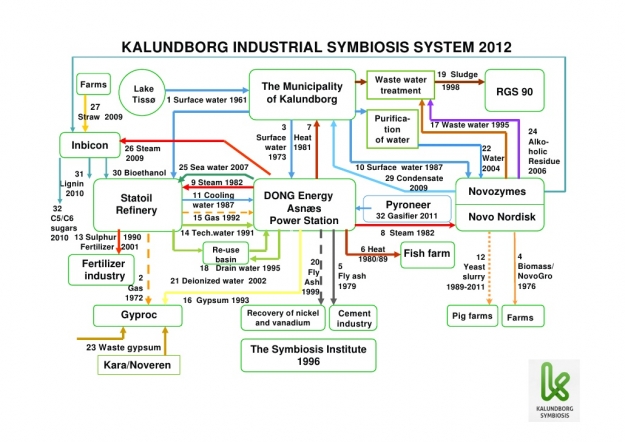
At the centre of Kalundborg’s spider web of intertwined industrial facilities lies the DONG Energy Asnaes Power Station, a 1500 megawatt coal fired power plant. Kalundborg is the birthplace of the idea of industrial symbiosis.
2018 UPDATE: The company is now called Greenfield Global and Truly Green Farms 45 acre greenhouse is now half heated by waste heat from the plant. Also see new story on Truly Green Farms
It’s called industrial symbiosis and it all started with their giant coal-fired power plant. Alongside all of those megawatts is excess steam, heat, gypsum and waste water and every single one of those byproducts have found a use in a complex ecosystem of industrial facilities around it.
Corn fuels cars, cows and tomatoes in Ontario industrial ecosystem
And it’s in this vein that we headed to Chatham, Ontario to see industrial symbiosis in action. Our catalyzing project in this case is Greenfield Specialty Alcohols, formerly called Greenfield Ethanol. It’s a first generation ethanol plant, a biorefinery that uses corn as a feedstock to produce 200,000 million litres of ethanol a year. Their production is split evenly between ethanol that is mixed with gasoline for vehicles and industrial ethanol, which you find in everything from shaving cream to vodka.
This refinery doesn’t just produce ethanol however, it kicks out a cornucopia of byproducts which they’ve found a number of uses for.
“Corn is a wonderful product because from corn, after the ethanol is made, with the sugars and starches that we convert there is a whole series of products that come from the fermentation,” says Angelo Ligori, the plant manager at Greenfield.
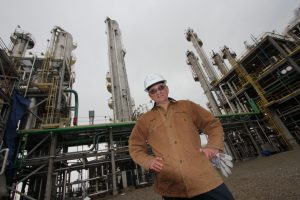
Angelo Ligori, plant manager of Greenfield Specialty Alcohols
Greenfield sells 140,000 tonnes of distillers grain, the leftovers from the ethanol fermentation process, as animal feed. There is a Praxair carbon dioxide facility onsite capturing and selling 100,000 tonnes of CO2 a year. Greenfield even produces 3-4,000 tonnes of industrial corn oil that is sold as a feedstock for animals or biodiesel feedstock.
But Greenfield has one more untapped waste stream. The plant’s smoke stack is a landmark in Chatham, Ontario and every day waste heat from drying their distiller grains shoots right out into the atmosphere. It turns out there is enough heat coming out of that smoke stack to provide the majority of the heating for giant greenhouse next door.
Fresh green tomatoes – from the smoke stack to your table
When you walk into the Truly Green Farm’s greenhouse the smell of tomatoes is heavy in the air. When I comment on it, Greg Devries, the president of Truly Green quips: “You like tomatoes? The right answer is yes. Everybody loves tomatoes.”
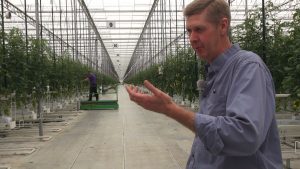
Greg Devries, president of Truly Green Farm’s greenhouses that plans to use the waste heat from an ethanol plant to heat 60 acre of greenhouse.
The greenhouse is huge, 22.5 acres with plans to expand to 90 acres and it’s chock full of green tomatoes on the vine that will ripen up shortly. Truly Green is slated to produce 5.85 million kilograms of tomatoes this year in this new building which has only been growing tomatoes since July of 2013.
Their location across the street from Greenfield is no accident. The plan is to take nearly all of the waste heat and leftover CO2 from the ethanol plant and use it to grow tomatoes. There are pipes underground that will bring hot water over to a heat exchanger and send cold water back on a loop. They expect to turn this system on in the next 12 months.
While Truly Green Farms is currently running two 1.25 megawatt natural gas boilers when they turn on the waste heat project it will cut their heating costs by 50 per cent. And when heating is 40 per cent of your total expenses that really helps the bottom line.
“It’s really a feel good story on a whole lot of different fronts,” says Devries as he explains just how tangled this amazing spider’s web of industrial integration is. Devries family farm operation is called Cedarline Farms and they produce corn, soybeans and wheat and they have a small beef feedlot operation.
The family farm sells corn to Greenfield Specialty Alcohols and buys distillers grain back to feed their cattle. Now they will take the heat and CO2 produced from making ethanol out of their corn to heat the Truly Green Farms greenhouse and to improve their tomato yield.
“Anytime I am going down the road and I see a stack coming out of a processing plant and I see steam coming out of it I say there is probably an opportunity somebody should be looking at,” says Devries.
Looking at smokestacks as opportunities instead of eyesores is how an industrial society thrives in the future and it’s also how you grow a greener, more energy efficient tomato.
Sidebar: Waste CO2 finds a use as well
Tomatoes love CO2, it’s like airborne plant food. Truly Green currently harvests CO2 off its natural gas boilers. However, in the summertime when there is little need for additional heat they don’t have access to CO2 – the pipe from Greenfield solves that. The CO2 is leftover from Praxair and would otherwise just be vented to the atmosphere.
“We are going to be able to get a stream of CO2 whenever we want it, all the way through the summer time. We will be able to increase the levels of CO2 to the greenhouse at levels that have never been achieved before and then hopefully get a three to five per cent increase in yield,” says Devries.
Using the waste heat and the waste CO2 Devries sees a marketing opportunity for a “green” tomato. He’s betting that consumers will pay a premium for a more energy efficient, local tomato.